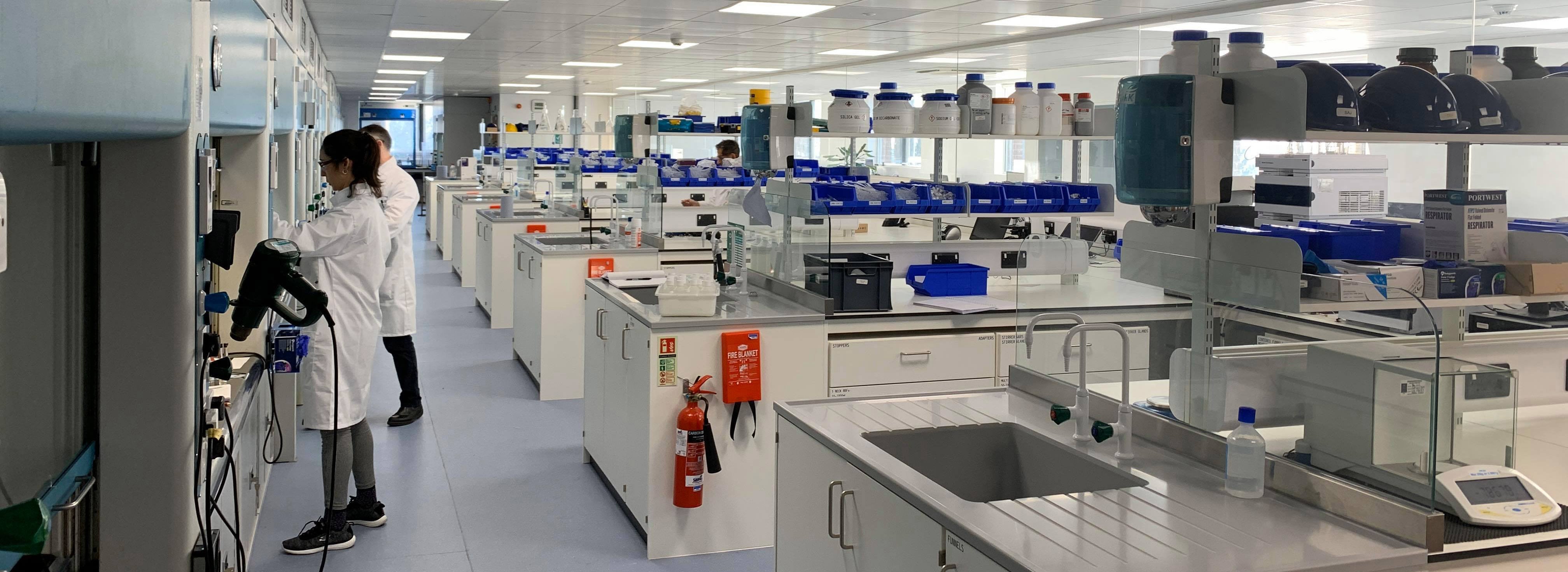
Development and Scale-up of a Miyaura Borylation Process
A joint effort of CARBOGEN AMCIS and Takeda Pharmaceutical - Dr. G Elena Daia (Process R&D Team Leader) at CARBOGEN AMCIS Ltd.
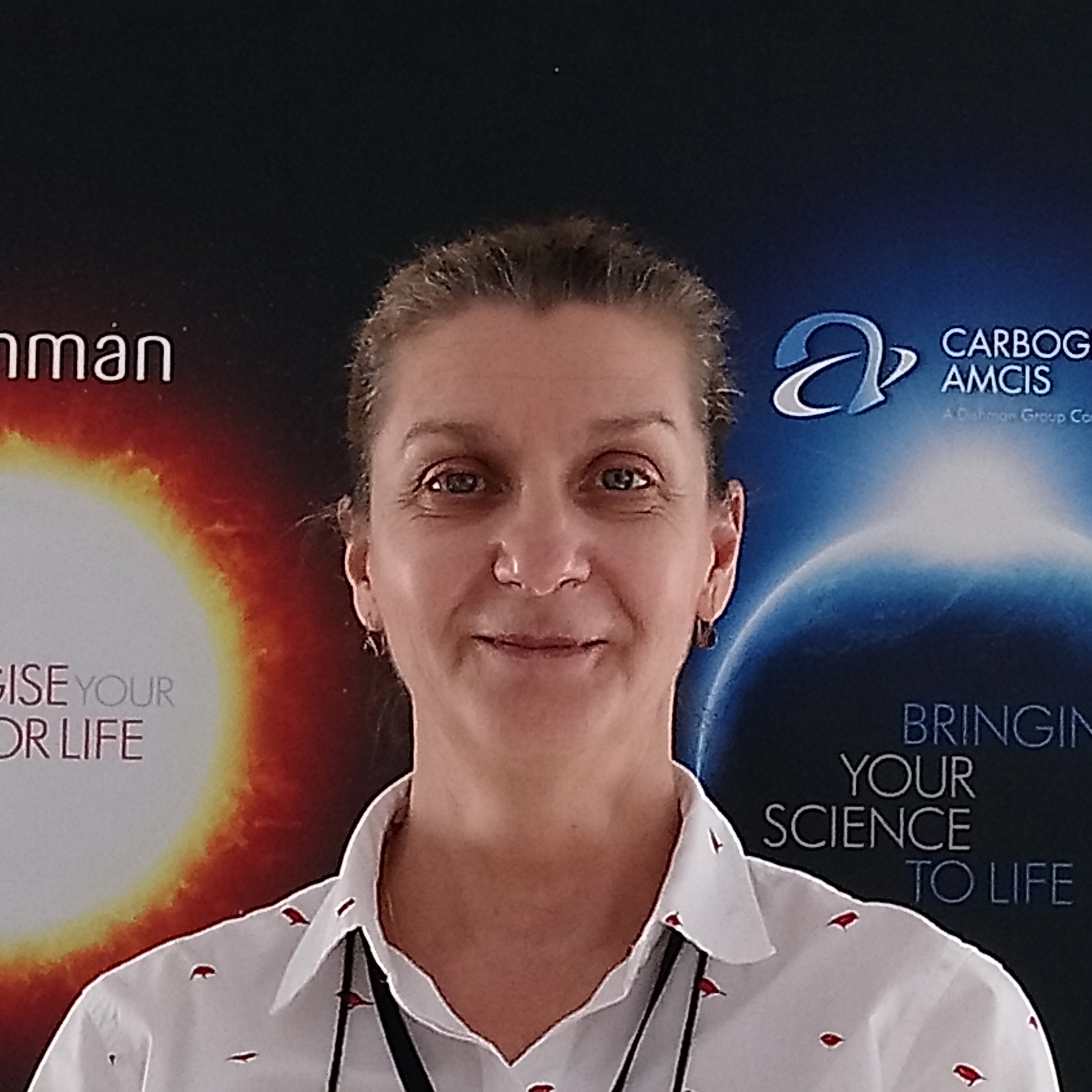
CARBOGEN AMCIS Ltd (Manchester, UK) is a Contract Development and Manufacturing Organisation (CDMO) and has over 30 years’ experience in the chemical industry. CARBOGEN AMCIS Ltd. is dedicated to the development of robust, efficient and safe processes for the manufacture of commercial quantities of high quality goods utilising appropriate quality standards. Products include regulatory starting materials for pharmaceuticals, cosmetic ingredients, materials used in the micro- electronics industry and other speciality fine chemicals. Projects undertaken may involve route scouting and analogue synthesis, as well as process development allowing operation at lab scale, at kilo lab scale and up to multi-tonne production scale. The following case study is one example of how CARBOGEN AMCIS helps customers to advance their projects with a dedicated team and state-of-the-art techniques.
Development of a revised Miyaura Borylation process
A modified Miyaura Borylation process was developed at CARBOGEN AMCIS Ltd. (Manchester, UK) using tetrahydroxydiboron instead of bis(pinacolato)diboron, obviating the need to hydrolyse the resulting boronic ester to its corresponding acid. The process was greatly simplified and successfully scaled-up from the laboratory to production; 65kg of the target compound was prepared, with reduced plant cycle time, resulting in a 47% overall cost reduction. Over the course of work, process sensitivity to oxygen was defined (though an in situ dissolved oxygen sensor) and allowed for optimisation of the amounts of tetrahydroxydiboron and catalyst, the key cost drivers.
Boronic acids are extremely useful reagents in organic chemistry, commonly employed as building blocks and intermediates. They are widely applied in cross-coupling reactions (e.g. Suzuki reaction) and are also of great interest in medicinal chemistry (e.g. Bortezomib).
The two main approaches to boronic acids are:
1. Metal-halogen exchange of the corresponding halide with an organolithium or organomagnesium reagent followed by quench with trialkyl borate; subsequent hydrolysis yields the boronic acid. This method has limitations as metal-halogen exchange and typically requires highly basic organometallics which are incompatible with many functional groups.
2. Transition metal-catalysed borylation which allows functionalization of both aliphatic and aromtic halides via organopalladium intermediates, with much higher functional group tolerance.
Case Study (Org. Process Res. Dev. 21 65 (2017)
Sing R. Gurung, Christopher Mitchell, Jie Huang, Marco Jonas, Josiah D. Strawser, Elena Daia,
Andrew Hardy, Erin O'Brien, Frederick Hicks and Charles D. Papageorgiou)
The target boronic acid 2 is a key starting material of “TAK-117” – a selective P13Ka inhibitor in Phase 1b clinical trials.
The first approach was a metal-halogen exchange: Boc protected aryl bromide (1) is treated with sec-BuLi, then quenched with B(OMe)3; subsequent hydrolysis should yield (2). However, it was found that under a wide range of conditions proto-debromination was dominant, suggesting an internal quench by the NHBoc. Since lithium halogen exchange between sec-BuLi and aryl bromides is invariably extremely rapid, metallation with lithium was deemed an unsuitable strategy for borylation. The alternative was Miyaura Borylation.
The process was developed using bis(triphenylphosphine)palladium(II) catalyst (1 mol%) and B2pin2 (1.1eq) with KOAc (3.0eq) as base and remained remarkably unchanged through to production. The reaction was conducted at 95-105oC for 1.5-2hr and performed on 20-50kg scale (5 process batches in total). The overall process was approx. 9.25 days for all unit operations. Although product of good quality was isolated (95.8-97.5% purity), yields were variable (60-75%) and significant debrominated (3) and homocoupled (4) impurities were observed from in-process controls (7-13%).
Problems surfaced when trying to determine reaction completion as boronate hydrolysis was reversible, and stalling of the reaction was also seen. This caused reactions to be stopped prematurely (variable conversion) and additional catalyst and were B2pin2 needed for full conversion.
Adapted reaction parameters & conclusions
It is apparent there was scope for process improvements to develop a more atom-economical,
higher yielding and robust process. A number of parameters were considered:
Boron source – to circumvent costly B2pin2
Pd catalyst
Stability of relevant boron reagent
Effect of ethylene glycol
Effect of oxygen
Effect of agitation rate
High-throughput screening was performed in the Radleys Carousel Reaction Station; thereafter intermediate laboratory experiments were done in standard laboratory glassware.
HPLC was adopted for IPC and final product analysis, 11B NMR for boron studies and oxygen sensors by Mettler-Toledo for dissolved oxygen and head space oxygen determination.
Overall, the process could be improved as shown in the table below. Additionally, a total cost saving of 47% based on proprietary CMO cost information over the original process could be achieved.