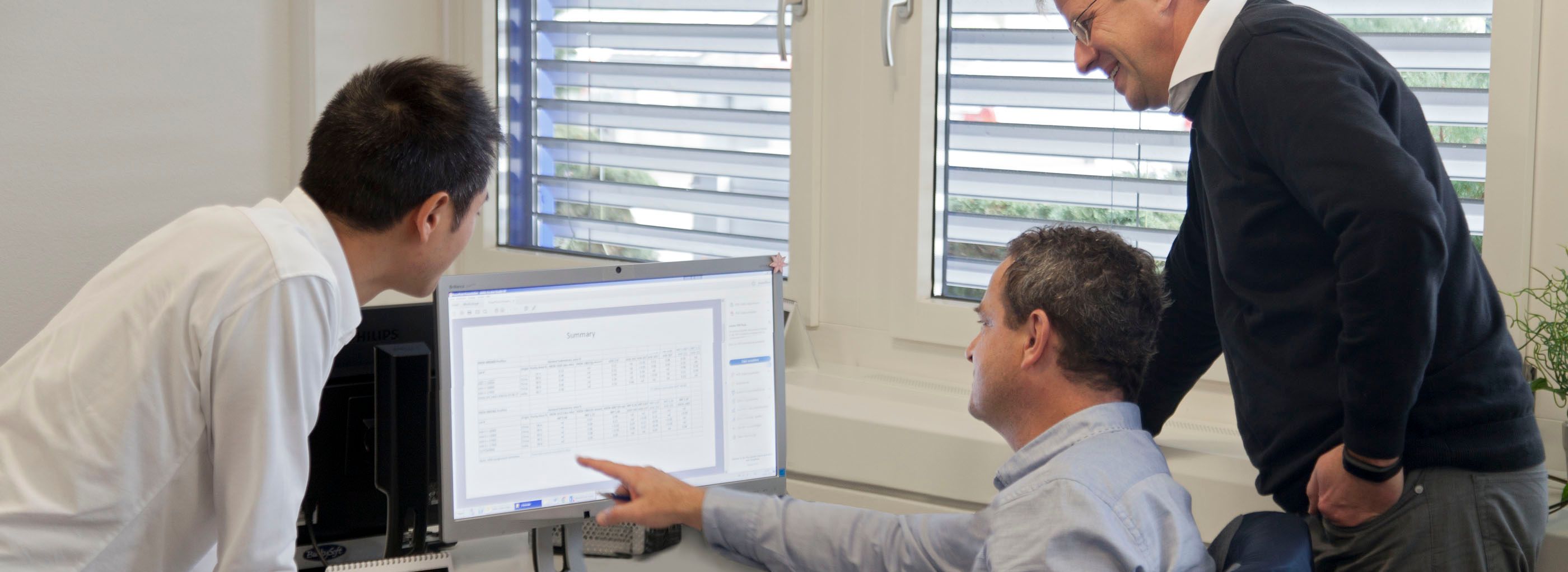
Solving Problems at CARBOGEN AMCIS towards Lean PDCA (Plan Do Check Act) and A3-report methods
The A3 method is a systematic approach to problem-solving widely used within the Lean philosophy. It gets its name from the A3 paper format, which is the standard size used for reports.
A3 report history
Developed by Toyota in the 1940s, A3 thinking became synonymous with the company’s approach to problem-solving. The A3 format was chosen for its practicality, similar in size to a tabloid sheet.
Toyota believed that any problem should be explainable and solvable using just one sheet of paper. The A3 process was used to document and facilitate PDCA (Plan-Do-Check-Act) quality improvement initiatives. Over time, it evolved beyond a simple tool into a profound method for managing and developing people within Toyota.
In the late 1970s, Toyota invested in developing the capabilities of mid-level managers through the Kra-Pro program (Kanri Nouryoku Program). This initiative aimed to foster a Lean culture among managers and employees and was structured around the A3 process, recognizing its effectiveness.
The A3 Report has since transcended Toyota and is now widely used globally across industries worldwide. Its concise format encourages clear communication, collaborative problem-solving, and ownership.
What is the A3-report methodology?
The A3 method is a management tool that guides the problem-solving process in seven steps, on a single sheet of A3 format paper.
The 9 Steps of the A3-report:
- Problem description and team building: Clearly define the problem and understand its impact on the business.
- Analysis of the Current Situation: Collect data and analyze the current process to understand where and how the problem occurs.
- Goal Setting: Define what you hope to achieve by solving the problem.
- Immediate actions (if needed): Take any necessary immediate actions to mitigate urgent issues before proceeding with long-term solutions.
- Root Cause Analysis: Identify the fundamental causes of the problem using tools such as the Ishikawa fishbone diagram and the powerful 5 “Why” questions.
- Countermeasure Development: Propose and evaluate solutions to address the identified root causes and provide an explanation for the chosen countermeasures.
- Countermeasure Implementation: Implement the proposed solutions by following a plan and tracking their status.
- Evaluation of the results and the process: Track the outcomes of the implementation and evaluate the effectiveness of the countermeasures. This step clarifies the success or the failure factors.
- Follow up and Standardization: Based on the evaluation, either define a new standard that will be continuously improved or plan new countermeasures if the target is not reached.
What is the relation between PDCA and A3-report?
There is indeed a strong parallel between the A3 method and the Plan-Do-Check-Act (PDCA) cycle, another key tool in the Lean methodology.
The A3-report below shows how they align in their structure:
The A3 report is a document that embodies the PDCA process. It provides a structured template for undertaking each phase of the PDCA cycle and for communicating the results in a clear, concise manner. This makes it an invaluable tool for problem-solving and continuous improvement.
What is the use of A3-report tool and what are the benefits for CARBOGEN AMCIS?
The A3 method has proven to be versatile and effective in a wide range of problem types. At CARBOGEN-AMCIS, for instance, this methodology has been successfully applied in diverse types of problem solving with multiple benefits:
- Improving product quality and chemistry process robustness:
A3 thinking is commonly employed for analyzing deviations. When faced with an issue, we utilize the A3 format to document the understanding of the situation, investigate root causes, and propose effective countermeasures to tend to a most robust process with the lessons learned.
⮕ This structured approach saves valuable time and enables teams to address issues more efficiently. The A3 report provides a structured framework that ensures all relevant factors are considered and the problem is thoroughly analyzed. Once the root cause is identified, the problem can be solved with accountability, the new standards are defined (Standardization), to prevent the recurrence of the same issue. Documenting the problem-solving process can also be useful for training and/or future improvement(s) (Sustainability).
- Improving internal Standard Operation Processes:
The A3 method has helped us to streamline and enhance standard operation processes, leading to increased efficiency and productivity from our internal company processes, such as processes with multiple departments interfaces.
⮕ The A3 report serves as an effective communication tool that allows the problem, analysis, and proposed solutions to be easily shared with others. This can facilitate collaboration and consensus-building. For instance, the A3 report encourages communication between different teams, for improving an internal process at the interface(s) with greater transparency, enhancing teamwork.
- Reducing energy expenses:
By identifying wasteful practices and proposing energy-efficient solutions, the A3 method has contributed to significant energy savings in our company. For instance, at the Vionnaz site, an A3 sheet was used to focus on each major energy consumption area. The project team collaboratively worked through the A3 format, identifying opportunities for optimization and implementing changes.
⮕ This approach introduces structure and efficiency, fostering the development of critical thinking skills within the team. It requires the problem-solver to deeply analyze the problem, identify root causes, and develop effective countermeasures, which may sometimes challenge the status quo.
- Improving document management:
The A3 method has been used to improve the archiving system, making it more organized and easily accessible.
⮕ The A3 report promotes a culture of continuous improvement by encouraging a systematic approach to problem-solving for all employees who would like to improve their workspace. It helps to turn employees' daily issues into potential for improvement by analyzing the problem deeper.
These examples demonstrate the broad applicability, effectiveness, and benefits of the A3 method in addressing several types of problems in our business context.
What about the time to be invested in the A3 report tool?
The time required to complete an A3 report can vary depending on the complexity of the problem and the level of detail required. However, it is important to note that the A3 method is not just about filling out a form, but about fostering a systematic, fact-based approach to problem-solving in team collaboration. While the process might seem time-consuming at first, especially during the problem analysis phase (“Plan” from PDCA), the long-term benefits can far outweigh the initial time investment. As shown on the previous graph, the planning phase is the most time-intensive. Once this phase is complete, the solution is typically clear, making the subsequent phases much easier—like reaching a summit before descending.
“A problem well stated is a problem half-solved.” - Charles Kettering
The A3 method is a powerful tool for solving problems in business. It encourages a systematic and collaborative approach to problem-solving, while promoting a culture of continuous improvement. Though it may require an initial time investment, its benefits (in terms of improved problem-solving, communication, and continuous improvement) can make it a valuable tool for any organization. Keep improvement going!
Julie Walter, Project Chemist PR&D
Patrick Gay, Manager PR&D