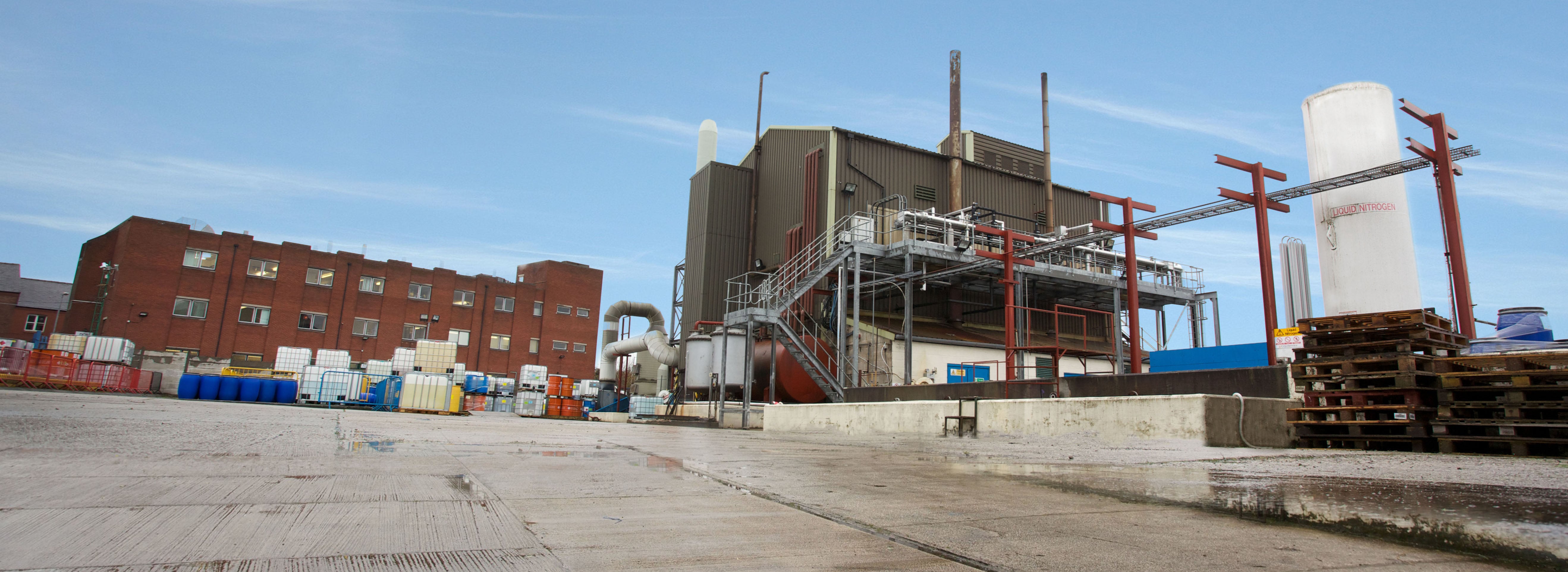
Custom Development and Manufacture of Fine Chemicals
An insight by Robert Rhodes - Director Operations at CARBOGEN AMCIS Ltd.
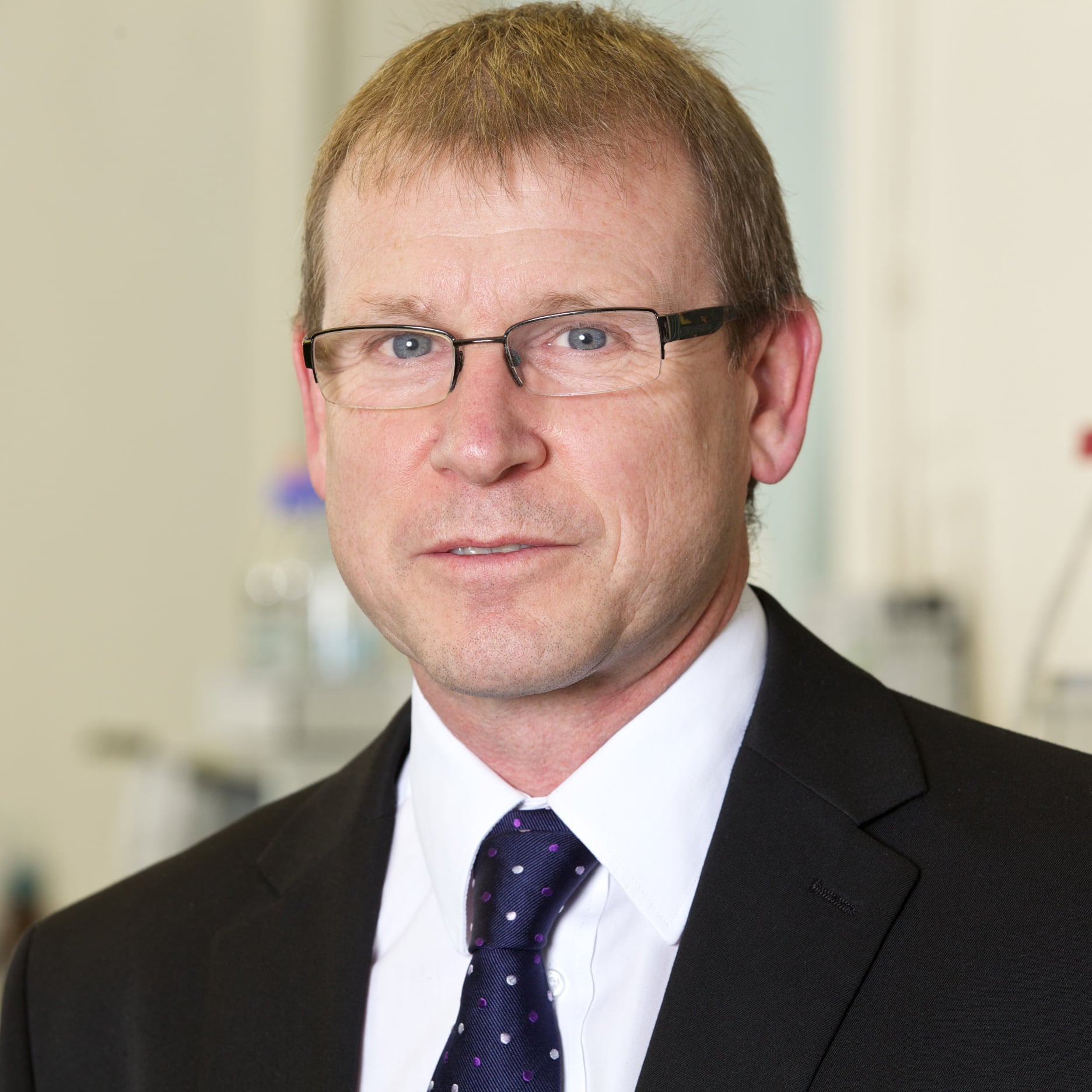
CARBOGEN AMCIS Ltd (Manchester) is a Contract Development and Manufacturing Organisation (CDMO) and has over 30 years’ experience in the chemical industry and is dedicated to the development of robust, efficient and safe processes for the manufacture of commercial quantities of high quality goods utilising appropriate quality standards.
CARBOGEN AMCIS Ltd (Manchester) is a Contract Development and Manufacturing Organisation (CDMO) and has over 30 years’ experience in the chemical industry and is dedicated to the development of robust, efficient and safe processes for the manufacture of commercial quantities of high quality goods utilising appropriate quality standards.
Products include regulatory starting materials for pharmaceuticals , cosmetic ingredients, materials used in the micro-electronic industry and other speciality fine chemicals. Projects range from pure route scouting to process development to synthesis of a range of analogues on very small scale to laboratory scale synthesis to kilo laboratory production to large scale production on multi-tonne scale.
GMP or non-GMP?
Although “cGMP“ and “non-GMP“ are commonly used terms within the pharmaceutical industry, it should be more accurately termed “appropriate-GMP“ since even “non-GMP“ production requires many cGMP concepts to be considered in order to achieve a robust and dependable quality standard. However, the GMPs do become more stringent as the final drug product is approached. The GMPs being applied should be appropriate to:
1. The phase of drug development. It is not a regulatory expectation to apply the same level of cGMP to a new drug in clinical trial (IND in US, IMP in EU) as it is to a marketed drug product.
2. The stage in the synthesis of the drug product. For example, the manufacture of very basic chemicals require less control compared to regulatory starting materials where stringent precautions such as control of process modifications, reagents and / or specifications for earlier intermediates might be appropriate. The API or final drug product require very stringent GMPs.
ICH Q7 Indicates
Designated Regulatory Starting Materials is not included within ICH Q7, but especially impurity profile has to be carefully considered (ICH Q11 and recent EMA reflection paper). Full GMP regulations are applied from when the Regulatory Starting Material is introduced into the process leading to the final API. However, even non-pharmaceutical products require high quality standards to be followed. The approach taken to the Quality Management System at the CARBOGEN AMCIS Manchester site has been to follow a GMP standard suitable for cosmetics - the ISO standard ISO22716:2007 (Cosmetics - Good Manufacturing Practices). This quality standard was chosen since CARBOGEN AMCIS Ltd has been developing and manufacturing cosmetic ingredients for over 20 years with a dozen cosmetic ingredients in development and/or production.
The Quality Management System supports the current and future cosmetic ingredients portfolio. Moreover, it provides the basis for all of the products manufactured at the Manchester site and is not restricted to only cosmetic ingredients. Since the standard is closely aligned to the GMPs for pharmaceutical excipients, it is also appropriate for the pharmaceutical-related productions being performed at Manchester.
Implications for Process Development & Manufacture of Regulatory Starting Materials
In past years GMP requirements have had relatively little impact on the development and manufacture of pharmaceutical intermediates up to and including Regulatory Starting Materials (RSM).Simply stated, it was expected that the RSM should contain a significant structural portion of the API, there should be a reasonable number of chemical steps before the API is reached and a specification should be in place that adequately describes the quality of the material. Other factors, such as being a commercially available commodity chemical with non-pharmaceutical uses, were also considered.
In more recent times, there have been increasing demands put on the RSM manufacturers as a result of many factors including
1. Increasing complexity of APIs results in increasing complexity of the RSM (“all the simple drugs have already been invented“)
2. Partly as a result of the above factor and the consequent increase in cost of development and manufacture, but also because of the perceived willingness of regulators to agree to RSM designations presented to them, the RSM was being defined ever closer to the API.
3. Increasing awareness of Potential Genotoxic Impurities being introduced into the API through the RSM.
4. Quality by Design approach being promoted at all stages of process development.
5. Analytical instrumentation becoming more sensitive and specific and resulting in specifications becoming more detailed and defining lower detection limits.
6. In 2014 the European Medicines Agency (EMA) published a reflection paper (up-dated in 2017) on requirements for selection and justification of starting materials of chemical active substances which represented an increase in the expectations for the justification of the syntheses of proposed RSMs. In this case more information is now expected on the level, source and fate of impurities.
Challenges for Process Development and Manufacture
Most of the challenges faced for non-GMP Development and Manufacture of pharmaceutical intermediates will be familiar to all service provider CDMOs, irrespective of GMP status.
By the very nature of the pharmaceutical industry, timescales are of the utmost importance. Whether this is owing to an effort to be the first to market in a particular field of application for commercial reasons or the desire to fulfill an unmet need as quickly as possible, pressure is always present on available time. However, a fast delivery also has to be matched by the quality and quantity of product.
All manufacturing operations have the target to deliver on time and in full (OTIF) and it is this reliability of delivery with constant quality that all customers value most.
The challenges faced in meeting this requirement could be of a technical nature where very often a newly developed chemical process is being scaled up for the first time, a need to deliver within a budget or a need to deliver within a certain timeframe. All of these factors often combine such that the requirement to provide sufficient data related to the chemical process (for example yield, quality, stability, robustness, safety etc.) prior to manufacturing starting require a high level of resource to be assigned to the project.
In order to meet with the increasingly stringent requirements, it is necessary for a CDMO operating under “non-GMP“ conditions to be well equipped with the necessary laboratory equipment, process equipment, analytical equipment and the required number of skilled and experienced process and analytical chemists, but also the systems to control impurities and deliver constant quality.
As a CDMO service provider, CARBOGEN AMCIS Ltd has worked over a long time period with a wide variety of products, chemistries and clients. This wide ranging experience provides the ideal situation to provide an efficient and cost effective service. This service offering is enabled by both the breadth and depth of technical knowledge and experience of our people.
In recent years, significant investments have been made at the CARBOGEN AMCIS Manchester site to meet the needs and expectations of the market. This has included the recruitment and training of additional people, a revised organization structure, process and analytical development facilities, infrastructure improvements (offices, laboratories, production, warehousing and maintenance), production equipment and services.
Process Development Facilities at CARBOGEN AMCIS in Manchester
For Process Development at CARBOGEN AMCIS in Manchester, there are 24 fume hoods available for Process Development and 6 fume hoods for Kilo laboratory experiments. Other equipment includes parallel processing reactors (including Integrity 10), Pressure Hydrogenation screening apparatus, a range of parallel reactors suitable for DOE process optimisation and a comprehensive process safety laboratory
Analytical Development Facilities
For analytical development at CARBOGEN AMCIS in Manchester we have a comprehensive suite of analytical equipment including HPLC and UPLC (UV, DAD, CAD detection), GLC (FID and Headspace) and LC-MS and GC-MS (vital for impurity profile tracking to support fate of impurity studies resp. impurity identification on intermediates and our products) and others including ICP-OES and NMR. The analytical suite allows us to offer a wide range of services including method development and validation, characterization/structure elucidation, impurity profiling and tracking. Our facilities enable us also to perform stability / stress testing (non-ICH) to provide real world storage and shelf-life data.
Facilities for Manufacturing
The Production plant is designed and built to a highly multi-purpose philosophy with maximum
flexibility built in. This is of the utmost importance since a service provider has to have the capacity and facilities that can handle a very wide range of processing scenarios:
1. The size of reactors in the Manufacturing operation start from 85L and go up to 4500L in
a range of materials of construction including glass, glass lined mild steel, stainless steel
and HastelloyTM.
2. Temperature range in Production from -80°C up to 200°C with a pressure range from full
vacuum to 3 bar.
3. Options for filtration include Vacuum and Pressure Nutsche filters, Filter Press, agitated
filter-dryers.
4. Options for drying include vacuum rotary cone dryer, vacuum tray dryer, agitated pan
dryer, agitated filter dryers
5. ISO Class 8 cleanroom (equivalent to FS 209E Class 100,000) available for controlled
handling of materials
Facilities for Safety Appraisal
Safety of operation is of paramount importance. Chemical production always involves some
element of risk with the spectrum ranging from almost no risk to being so dangerous as to be
practically impossible to operate. Therefore, the assessment of risk has to be very carefully considered and be based on sound data. Some data is well known and quite simple to obtain (e.g physico-chemical data such as boiling point, flash point etc.). Other data, such as a full range of health hazards, are often not available at the stage of development often encountered in our industry and read-across data and SAR predictions are often used. CARBOGEN AMCIS utilises a categorisation system which considers a number of factors such as potency, OEL range, Oral Toxicity and assigns a Category number ranging from 0 to IV with 0 being the lowest. Occupational Hygienists and Toxicologists provide advice on the appropriate categorisation. At the extreme, operations are only possible under conditi¬ons of high containment. CARBOGEN AMCIS Ltd, as a standard, can operate down to an OEL of 10μg/m3 8h-TWA.
CARBOGEN AMCIS Ltd has an extensive range of chemical process safety testing equipment that isutilised to provide data on which a process risk assessment can be based. The available in-house testing facilities include:
SETA closed-cup flash point tester
DSC to provide melting point data and stability data
HEL Phi-TEC II to provide classical TSu / DSC-type data but with added gas evolution measurement, adiabatic ARC-type data and also low-phi factor adiabatic calorimetry
HEL Simular to provide reaction calorimetry data (heat flow and power compensation), modified to also allow direct measurement of evolved gas generation
In addition to the above on-site facilities, the CARBOGEN AMCIS safety service at Aarau can also
provide support for ARC, RC1 and fall hammer testing.
A combination of these and other testing techniques allow a suitable Basis of Safety to be
established. There are occasions where an adequate basis of safety cannot be established - in these circumstances, an alternative safer process is developed.
Project Progression from Enquiry to Delivery
It is quite typical for CARBOGEN AMCIS to receive an enquiry from a potential Client which
comprises the following scope:
1. Description of a process chemistry on small laboratory scale
2. Provisional specification of final product
3. Delivery schedule including Quantity and Timeline
Very often important required information is not available at the time of the enquiry, such as:
1. Raw Material Suppliers
2. Specifications of Raw Materials and Intermediates
3. Suitable analytical methods appropriate to the specifications
4. In-process, intermediates and final product stability data
5. Process robustness information (including the effect of small process changes that
inevitably occur in process scale up)
6. Process Safety Data
An initial evaluation of the available information is performed and a programme of process and
analytical development work to fill any data or knowledge gaps is compiled. A detailed proposal is prepared that includes all aspects of work that is required to enable a final product delivery.
The proposal will outline all aspects of the project deliverables and will include a cost breakdown
covering process and analytical development, raw material, production, analytical and delivery
costs. Although it is recognized that exact timings (and therefore costs) are problematic to estimate, especially where a process requires significant process-enabling development or where a chemical process is being scaled up for the first time, this is done on a “best effort“ basis and, where there are significant uncertainties, these are highlighted.
A project team is set up which typically includes an overall project coordinator, process
development chemist, analytical development chemist, production chemist and supported by the appropriate level of supply chain (sourcing/logistics etc.), QA and EHS. All individuals provide a vital input to the progression of the project from inception, through process and analytical development, production, quality control, release and finally delivery to the customer. In all cases communication is a vital component of a successful project. At any interface (for example between Customer Purchasing and CARBOGEN AMCIS Sales, or Process Development and Production) there is the potential for data loss or misunderstandings and this requires a high level of attention to detail.